Have you ever wondered what it takes to transform centuries-old barn wood into exquisite reclaimed flooring? Or why reclaimed barn wood flooring often carries a higher price tag than its new, mass-produced counterparts? The answer lies in a meticulous, labor-intensive process that honors the wood’s history while ensuring it meets the highest standards of quality and craftsmanship. Appalachian Woods has mastered this art, creating flooring that tells a story while delivering unmatched durability and character.
Here’s an inside look at the step-by-step process behind Appalachian Woods’ reclaimed barn wood flooring:
Sourcing Reclaimed Barn Wood
It all starts with locating and salvaging wood from old barns and historic structures slated for demolition or deconstruction. Appalachian Woods handles some of this reclamation directly and partners with a trusted network of contractors who specialize in careful salvage work. These contractors work closely with Appalachian Woods’ General Manager to deliver only the highest-quality reclaimed lumber suitable for flooring.
Reclaimed woods like oak, chestnut, and pine are among the most sought-after for their rich history and natural beauty. The challenge—and beauty—of this process lies in preserving the integrity of these materials, which have stood the test of time.
Cleaning and De-Nailing
Once the wood arrives at Appalachian Woods, the real work begins. Each board is thoroughly cleaned to remove decades of dirt, debris, and any residues from its previous life.
Next, nails, screws, and other embedded metals are carefully removed. This painstaking step is vital not only to protect the milling equipment but also to ensure the integrity of the finished flooring. De-nailing is one of the most labor-intensive parts of the process, requiring skill, patience, and attention to detail.
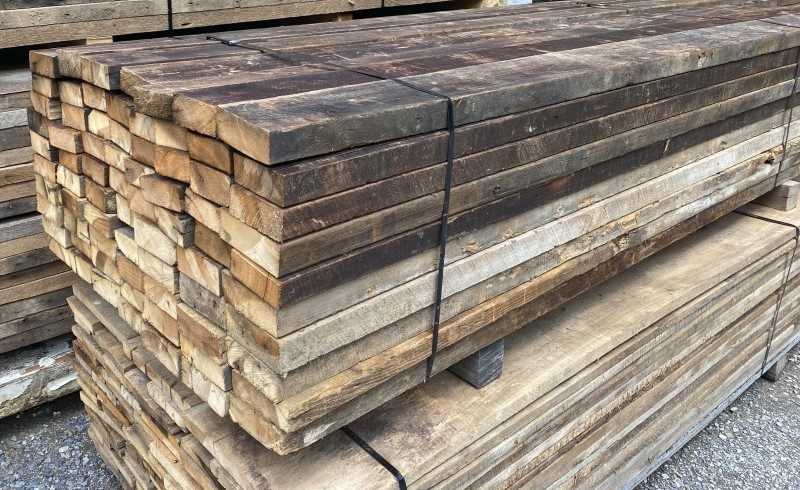
Kiln Drying: Preparing the Wood for Flooring
Even though reclaimed wood may be over 100 years old, it still requires kiln drying. Why? To ensure the moisture content is reduced to the ideal level for solid plank flooring. Proper kiln drying prevents warping, shrinkage, or expansion once the flooring is installed, ensuring it’s as stable as it is stunning.
Ripping and Straightening
Before the wood can be milled into flooring planks, it needs to be straightened. Using precision saws, the rough lumber is ripped and straightened along the edges to prepare it for milling. This step ensures consistency and precision in the final product.
Milling: Crafting the Flooring Planks
The cleaned, de-nailed, and kiln-dried lumber is now ready for milling. This involves cutting the boards to a uniform thickness and width, tailored to each project’s specifications. Appalachian Woods offers various milling profiles—such as tongue-and-groove or straight edge—depending on the desired installation method and aesthetic.
Quality Control: A Commitment to Excellence
Each board undergoes rigorous inspection both before and after milling. Appalachian Woods’ commitment to quality means that every piece of flooring delivered to customers is 100% usable. This reduces waste on-site and ensures customers can install their floors with confidence.
Some natural imperfections—like knots or saw marks—are embraced as part of the wood’s character, but defects that compromise durability or aesthetics are addressed or discarded. Appalachian Woods also provides detailed product spec sheets to help customers understand the unique characteristics of each floor, from the level of patina to the degree of original saw marks left intact.
Because every batch of reclaimed lumber varies, each floor is custom-milled and one-of-a-kind, reflecting the individuality of the wood itself.
Finishing: Protecting and Enhancing the Wood
While most finishes are applied on-site after installation, Appalachian Woods also partners with trusted finishers who can pre-finish the flooring if desired. Common finishes include natural oils, polyurethane, and water-based sealers, each selected to protect the wood while enhancing its natural beauty.
Custom finishes can also be applied to achieve specific looks, whether that’s a rustic matte patina or a polished, contemporary sheen.
Packaging and Shipping
Once the flooring has been milled, inspected, and (if requested) pre-finished, it is carefully packaged and prepared for delivery. Whether shipping directly to customers or retailers, Appalachian Woods ensures every order arrives in pristine condition, ready to install and enjoy.
Why Appalachian Woods’ Process Stands Out
This step-by-step transformation is what sets Appalachian Woods apart. Since 1997, this small family-owned business has dedicated itself to the art of reclaiming and repurposing historic wood into timeless flooring. Every floor is crafted to order, allowing Appalachian Woods to focus on the unique needs and vision of each customer.
Thousands of satisfied customers over the years have trusted Appalachian Woods to bring the beauty and history of reclaimed wood into their homes. From its meticulous sourcing process to its custom craftsmanship, Appalachian Woods turns yesterday’s barns into today’s heirloom-quality flooring.
To learn more about Appalachian Woods’ reclaimed barn wood flooring or explore their full range of products, visit Appalachian Woods. For more details and photos of our flooring, check out our Instagram and Houzz pages.
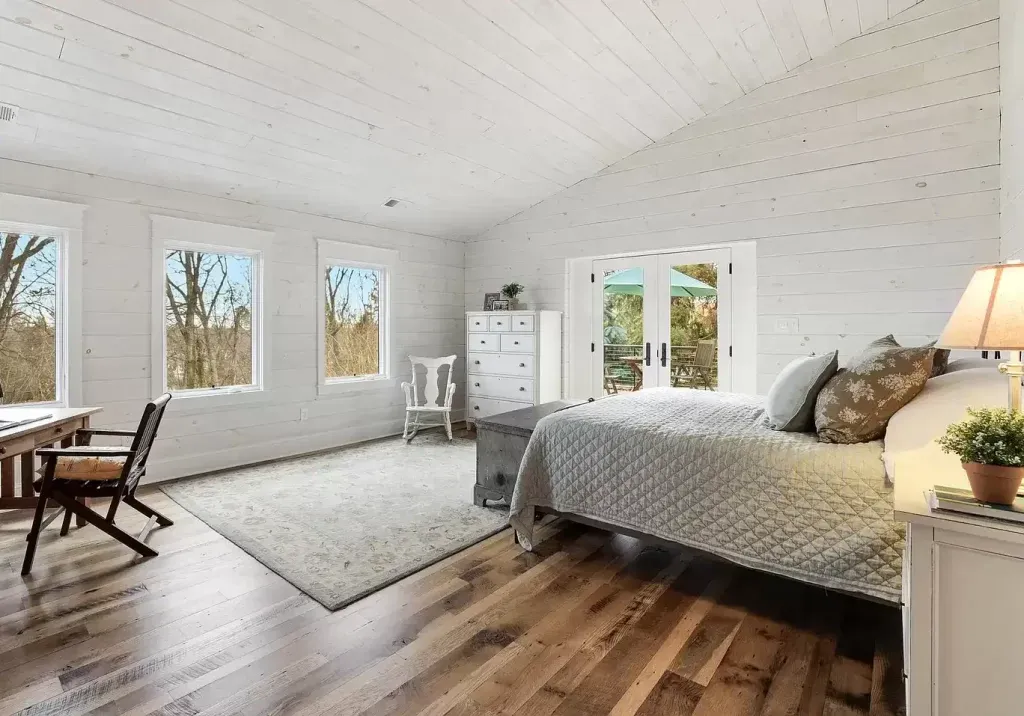